No.19
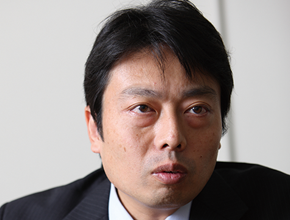
ナノ炭素材料の合成法確立と実用化を目指す
副産物の出ないナノ炭素繊維の合成法を開発
高密度な炭素繊維を生成し、多分野にわたる製品開発に役立てる
環境都市工学部エネルギー・環境工学科
中川 清晴 助教
Kiyoharu Nakagawa
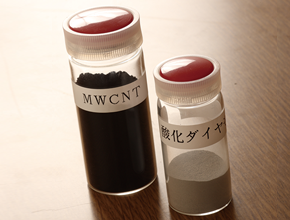
1960年代に出現した炭素繊維は、炭素材料の応用範囲を飛躍的に広め、工業的に様々な分野で利用されてきました。最近ではナノ構造を有する炭素材料が注目されており、その合成法の開発は発展途上の段階です。環境都市工学部の中川清晴助教は、マリモカーボンとカーボンナノチューブの新しい合成法を開発し、より効率よく高密度な炭素繊維を生成することで、製品開発の可能性を広げる研究に取り組んでいます。
新規炭素材料としてのカーボンナノチューブ
まず基本的なことですが、カーボンナノチューブとは?
鉛筆の芯などに使われているグラファイト(黒鉛)をベースとする構造をもつ繊維で、グラファイトは通常、ベンゼン環が平面上に並んだグラフェンシート(Graphene sheet)と呼ばれる巨大平面分子が積み重なった構造をしています。新規炭素材料のカーボンナノチューブは、基本特性はグラファイトと同じで、そのシートが筒状になっています。一枚のシートで包まれたものをシングルウォールナノチューブ、木の年輪のように層になっているものをマルチウォールナノチューブと言います。外見は同じナノサイズの繊維でも、生成法や触媒により中の構造を作り分けることができ、構造が異なることで性質も変わってきます。
どのようなものに応用されているのですか?
現在、盛んに研究されているのが燃料電池などの電極、キャパシタ、リチウムイオン電池、触媒担体、導電線あるいはトランジスターなどですが、物理的・化学的特徴を生かしきる製法で作るところまでは至っておらず、用途に関しても手探りの部分が多いのが現状です。
酸化ダイヤモンドを触媒とするマリモカーボンの合成
どのような方法で炭素繊維を合成するのですか?
酸化ダイヤモンドの粉体を触媒の核(担体)として使用します。Ni,Co,Pdなどの金属を酸化ダイヤモンドの表面に担持し、触媒流動気相合成装置を用いてメタン分解反応を行います。すると、ダイヤモンドを核に細かい繊維状の炭素が放射型にできます。これは天然のマリモと同じ構造をしているので“マリモカーボン”と呼ばれ、反応温度や時間を制御することで粒径を精密にコントロールできる可能性があり、大量合成も可能です。また、マリモカーボンは高密度にナノ炭素繊維が凝集されているため、切れて粉塵が散らばることもなく、化学物質の安全面からみても扱いやすいといえます。
触媒担体に酸化ダイヤモンドを使うメリットは?
酸化ダイヤモンドは表面を酸素に覆われており、その酸素が規則的に並んでいるという特性があります。酸素の部分にだけ金属微粒子が付いて高分散に保たれるため、高密度のカーボンナノチューブの生成が可能となるのです。また、内部のダイヤモンドはカーボンであるため、生成物に不純物が含まれることなく、仕込みに対して10倍もの量を生成することができます。
液層法による高配向カーボンナノチューブの合成
もうひとつの合成法は?
ビーカー内でカーボンナノチューブを生成します。アルコールや炭化水素などの有機化合物液体の中で、触媒を基板上に乗せて通電加熱する方法です。液層の中で作るので、基板の表面だけが800~1000℃となって赤熱し、その基板上を垂直にカーボンナノチューブが成長します。反応が速いため1分間で数μ成長し、電力は数十Wでしか要しません。
この方法で生成されたカーボンナノチューブは一方向に電子を放出するため、電界放出ディスプレイ(FED)などの電子放出源として使えるようになると考えています。
より高い選択率・転化率をめざして
開発した2つの合成法と従来の合成法の違いは?
従来の合成法であるレーザーアブレーションやアーク放電法などは、大型装置を使用し、大抵は反応管全体を1000~3000℃にする必要がありました。時間とエネルギーがかかるうえ、反応部以外でも勝手に熱分解が起こります。また、生成物のほとんどは副産物(スス)で、その中をより分けて精製・分離するなどのプロセスを要するため、効率が悪くコストもかかります。また、抽出したカーボンはふわふわとして嵩の割には重さがほとんどなく、g・㎏単位での入手は困難。生成物の向きも様々で、毛玉のようになっている場合もあり、大量生産や選択的に必要な場合には適しません。
紹介した2つの方法は大量生産が可能であり、触媒や反応条件を選定することで、副産物を極少量に抑えることができます。
高密度な炭素材料を提供し、製品開発へ
実用化に向けての課題と今後の展望について。
当面の課題は「製法を確立し、提供すること」です。カーボンナノチューブが世間に紹介されて10年経ちますが、未だ出回っていないのは大量生産ができていないということです。製法が確立していないものが多く、論文通りに合成しても同じ結果が得られにくい事実もあります。幸いにもこの2つの方法は、技術を訓練し、正確に操作すれば誰にでもできる合成法です。
カーボンナノチューブは軽量で優れた強度をもち、錆びません。現在使われている炭素繊維に代わることはもちろん、キャパシタや電界放出ディスプレイ(FED)材料、触媒担体、飛行機や自動車用部材、コンポジットへの応用など、多くの利用が期待されています。私たちは企業が求めている性能や用途も参考にして研究を進めていますが、製品開発の材料として必要としている人にカーボンナノチューブが行き渡っていないという現状をクリアすれば、用途は格段に広くなるでしょう。また、化学的な視点からだけでなく、異なるフィールドの人たちが発案する用途、材料の可能性も興味深いところです。研究者として社会における製品開発に貢献するためにも、さらに無駄なプロセスを減らし、低コストで効率のよい合成法を確立したいと考えています。